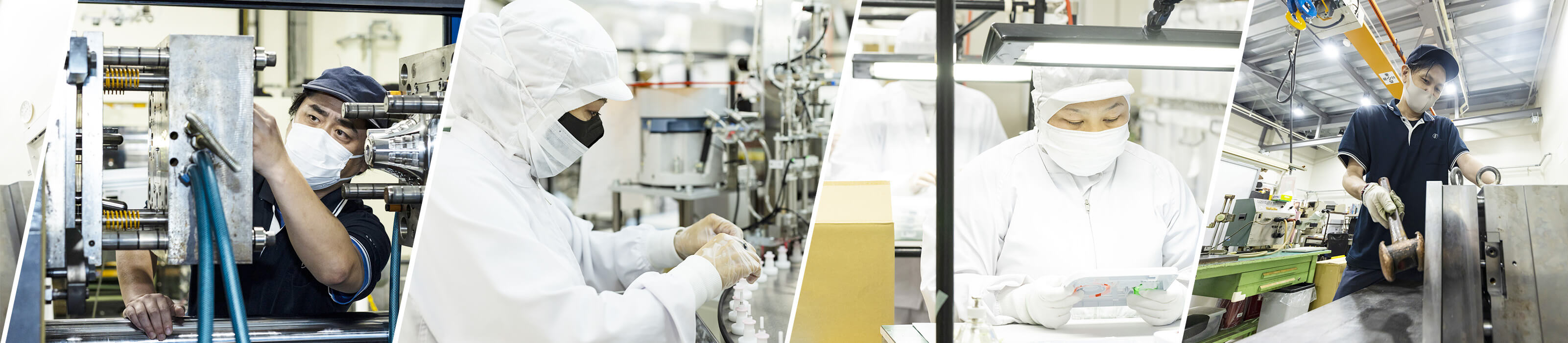
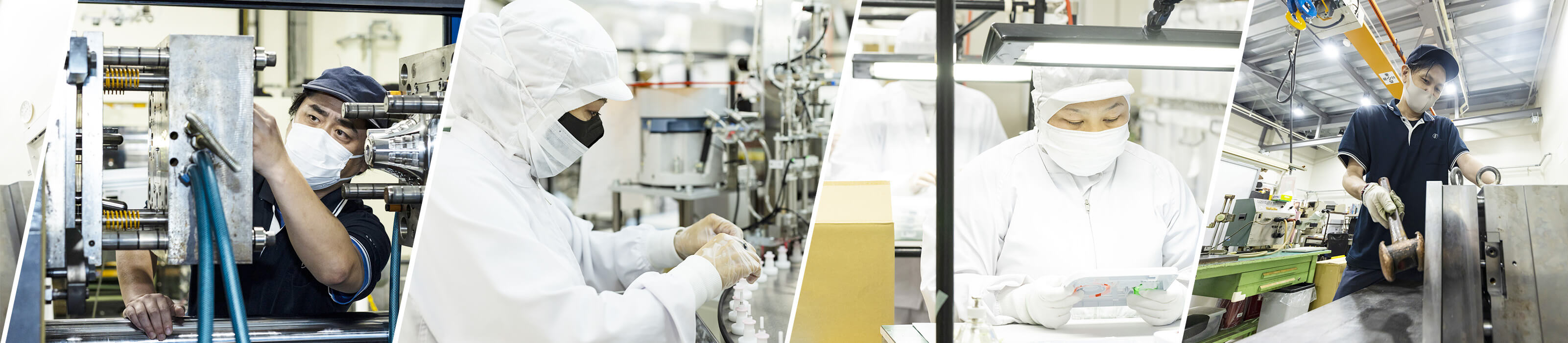
プラスチック製品の
ワンストップ・ファクトリー
富士合成
富士合成は、お客さまのご要望、条件に合わせて材料の選択から金型の設計・製造、成形、加工・組み立て、塗装、そして印刷までのすべての工程をお引き受けするプラスチック製品のワンストップ・ファクトリー。
プラスチック製品のことなら何でもお任せください。
一気通貫でプラスチック製品を製造
プラスチック製品を製造するとき、金型設計はA社、射出成形はB社、加工・組み立ては
C社というように分散して発注していると、手間もコストも時間もかかります。
富士合成なら、そうしたプラスチック製品の製造に関わる全工程を一気通貫に行っています。
したがってお客さまのご負担が軽減するのは確実。
一方で金型設計だけ、成形だけというご要望にも幅広くご対応しています。
もちろんすべての工程で高度な技術と優れた品質をお約束しています。
国内メーカーの高い要求にお応えする高品質
富士合成の創立は1941(昭和16)年。
以来、80年以上にわたりプラスチック製品の製造に取り組んできました。
そしてその間に蓄積してきた高い技術力と豊富なノウハウをバックボーンに、
大手電機メーカーや通信機メーカーなどの非常に高度なご要望にもお応えし、
お客さまから絶大な信頼をいただいています。